Flax, hemp, jute and ramie are "soft" bast fibers, fiber found in the stem of the plant. Jute is produced in the humid tropics. Ramie, a perennial nettle, although highly researched by the USDA, never became an established crop due to its recalcitrant degumming requirement.
Hemp fiber bundles are longer than those of flax, but flax fiber generally contains less lignin and is therefore more flexible and makes a finer fabric. The characteristics of these two fibers overlap and the best hemp can be superior to flax for fine fabric. Hemp is generally stronger than flax and both are stronger than jute. Hemp has been reported to yield twice the fiber of flax from an acre of land,14 but such comparisons are problematic. The yield, strength and quality of either fiber are highly dependent on the seed variety, the conditions of growth, time of harvest and manner of retting and other post-harvest handling.
The commercial hemp fiber ranges from 40 to 80 inches in length. The individual cellular fibers, which are organized in bundles to make the long, macroscopic fiber, vary from 0.19 to 2.16 inch in length and from 16 to 50 microns in diameter. Flax fiber length ranges from 6 to 40 inches, the cells from 0.43 to 1.49 inch in length and 11 to 20 micron in diameter.15
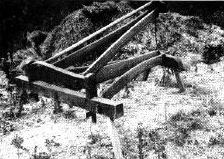
The production of high quality natural fibers is as much art as science. Since antiquity, bast fibers have been obtained by "retting" and "breaking" the stem. Retting (rotting) is the microbial decomposition of the pectins which bind the fibers to the woody inner core of the plant stem.16 In the US, retting has traditionally been accomplished by letting the cut stems lie in the field for a few weeks in the damp fall. Retting can also be done in pools or running water, which produces higher quality, lighter colored fiber, but can also create an odor and pollution problem from anaerobic decomposition. In Russia, some areas ret in the snow. The finest grades of hemp, such as the Italian, were produced by water-retting. The US Navy preferred water-retted hemp for its riggings:
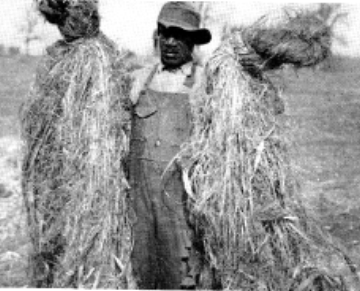
Water-retting never caught on in the US.
After retting, the fiber is separated from the woody inner core (hurds or shives) by "breaking," described as one of the hardest jobs known to man, hence, Thomas Jefferson's effort at bringing a degree of mechanical advantage to it. In 1896, Charles Dodge of the USDA Office of Fiber Investigations mentions that "nearly 300 patents have been issued in the United States for machines for breaking hemp, many of which have proved absolute failures...."18
The hurds are cleaned from the fiber by "scutching" and the fiber is further refined by "hackling" before being spun into twine and rope.
Flax and hemp, although botanically unrelated, have many characteristics in common. Without microscopic or chemical examination, their fibers can only be distinguished by the direction in which the they twist upon wetting: hemp will rotate counterclockwise; flax, clockwise. Flax is a dual usage crop, with linen varieties grown for their stem fiber, and other varieties for the oil in their seed. This is also true of hemp. Both plants produce very similar drying oils in their seed, oils with a high percentage of linolenic acid, used until mid-century in paints. The oils are also valued for nutritional and even medicinal qualities.19 Whereas linseed oil became a major industry, an industry based on hempseed oil was never firmly established in the US.20
Flax was called the "Pioneer plant" because it was the first crop grown on cleared land. However, it did not do well if grown successively on the same land. As a result, flax moved west with the Pioneer migration to Minnesota, North Dakota and the Canadian plains for the oilseed types, and to Michigan and Oregon for the fiber types. The decline in productivity when flax was grown repeatedly led to the belief that flax was "hard" on the soil, and it was not recommended to be grown more than once in ten years on the same land. Eventually, it was demonstrated that the poor performance was due to a Fusarium fungus that persisted in the soil and caused plants to wilt. Flax's struggle with a host of pathogens limited its progress. Today, the shortest recommended rotation for flax is four years.
Weed control in flax was also a problem. Hemp was sometimes grown the year prior to a flax crop because it left the land free of weeds and in good condition. Hemp, it was said, was "good" to the soil because it could be grown successively and improved the soil with its penetrating taproot. Although hemp demands substantial nutrition for growth, it has been estimated that greater than two-thirds of the nutrients used is returned to the soil when the crop is dew-retted.21
Additionally, hemp has often been grown for many seasons successively without deleterious impact on the soil. In fact, this is done on occasion to improve the soil tilth and clean land of weeds.
When cotton emerged as the dominant textile fiber, it competed more directly with flax than with hemp, as flax had been used for fine fabric and, "The cotton industry had considerable interest in hemp, since it was manufactured locally into baling cloth, rope and clothing for Negroes."22 But having been displaced by cotton as fabric, flax of coarser grade pursued hemp's non-maritime markets. Until 1872, a duty on imported jute protected the domestic flax and hemp industries. Its repeal that year was a concession to eastern manufacturing interests that opened the door to a cheaper raw material for bagging and set back the struggling domestic fiber industry. One flax worker saw it this way:
Today, we have lost sensitivity to the subtlety of natural fibers. But their differences and suitability for specific uses were an aspect of daily life to our ancestors. Since the time of George Washington, the government had tried to encourage domestic coarse fiber industries for baling cloth, twines, and cordage. Tariffs protecting the hemp industry were passed in 1789, 1816 and 1861.24 Hemp was a strategic material required for the shrouds, cables and sails of ships. However, most of the hemp used by the Navy was imported from Italy and Russia. For most of its history, the domestic crop's principal usage was for baling cloth to cover cotton bales. American hemp was dew-retted and therefore coarser than the European water-retted fiber. As much as five percent of the weight of a cotton bale was hemp.
In 1824, domestic hemp was pitted against Russian hemp by rigging the USS Constitution on one side with American and the other with Russian grown hemp, "and after being thus worn for nearly a year, it was found, on examination, that the Russian rope, in every instance, after being much worn, looked better and wore more equally and evenly than the American." But the commander said, "the difference between them was not so great as to warrant a declaration that the proof was conclusive in favor of the Russian...."25
Imported hemp continued to be favored by the Navy and domestic hemp was used only for twines and as oakum for caulking ships.26 Today, aficionados of ship restoration insist on authentic hemp oakum, witness the Alysha in Galveston harbor.
In 1878, New Jersey offered a bounty of $6.00 extra per ton of hemp stalks, $7.00 per ton for flax and $10.00 for ramie. But without tariff protection, the labor requirement for these fibers put them at a disadvantage against fibers produced using cheap labor in the tropics. Manila hemp, abacá, from a relative of the banana, took hemp's maritime markets. Rope made of this fiber did not require tarring, floated on water and was cheaper. By 1911, the nation was spending $16,000,000 importing tropical fibers. This drain on the economy had been recognized early on and in response the USDA ran several programs to promote domestic fibers and offered prizes for mechanizations.
Unable to compete with cotton, fiber flax production declined. But oilseed flax culture expanded. Due to chemical properties bestowed by its fatty acid composition, linseed oil was the principal ingredient of paints, varnishes and—after its invention by Frederick Walton in 1863–linoleum. The straw leftover from the oilseed crop yielded an inferior, coarse fiber that was usually burned. The flax industry needed an outlet for this byproduct: "With a present demand for 35,000,000 yards of bagging for cotton, while flax-fiber enough to produce it is thrown away, the effort to extend the production of flax bagging would seem to be worth official consideration."27
Displaced by cotton, in going after the baling cloth market, flax was displacing hemp, as was cheap jute:
The suitability of the fiber from oilseed flax varieties was a matter of some debate. According to some, "It is futile to expect that fiber and seed can be produced from the same crop."29 The Office of Fiber Investigations agreed, in 1893: "Seed culture and fiber culture are so distinctly different that the farmer who essays to grow fiber by the same methods he employs in growing seed can only make an ignominious failure and he will do well to avoid the experiment."30 Yet the market was there, materials were being imported, and the linseed indusry had a coarse byproduct suitable for burlap. The Flax and Hemp Spinners and Growers Association president, A. R. Turner, was optimistic: "it seems a safe statement to make that it is possible to preserve all the fiber from flax even though it may be sown primarily for seed."31
But flax fiber from the oilseed crop, as it came to the spinners, was of low quality and often dirty. As a byproduct, the quality of the fiber was given no priority and the method of harvest for seed left the stems tangled and soiled. Cotton producers did not care for it. In 1879, it was reported that the "New York Cotton Board will receive no cotton whatever baled with flax bagging, giving as a reason that flax bagging is so dirty it makes a difference in the price of the cotton."32
For fiber from oilseed flax to find a market, several technological developments were needed: "The special classes of improved machines demanded by this industry, in establishing an American practice, are (1) a flax-pulling machine to do away with the laborious and costly hand pulling; (2) an economical thresher, to save the seed without injury to the straw; and (3) an improved scutching machine to prepare the fiber for market."33
Similar technological developments were targeted for hemp, which the USDA was advancing aggressively. In fact, hemp yielded to mechanization more rapidly. In 1905, a mechanical hemp brake was "the first machine having sufficient capacity to be commercially practical that has cleaned bast fiber in an entirely satisfactory manner."34